Machine taps in BAER Online-Shop
If you're new to tapping and looking to buy a machine tap for the first time, the plethora of varieties on offer may be a little intimidating at first. The machine taps in our Online-Shop are highly specialized tools designed for specific cutting applications. This means the machine taps do their job with the utmost perfection and precision. At the same time, it also means that you have to find the right machine tap first.
But don't worry, together we'll get it done. Let's first clarify a few basic terms and then take a look at the various construction dimensions, chamfer forms, materials and coatings. This will clarify in no time which machine tap you should buy to successfully implement your project. And if you still have questions, please feel free to contact our friendly customer service at any time. There you can expect competent advice that you can rely on.
Structure of a machine tap
Each machine tap has certain characteristics that clearly distinguish it from other types. At first glance, the machine tap can be divided into shank and head. The shank may be of uniform thickness or may become thicker towards the end. In any case, it ends in a square.
The characteristic features on the head are the thread profile, the chamfer and the flutes. The thread profile specifies the type of thread and is defined by values such as the diameter, the flank angle and the pitch. The chamfer is at the tip of the machine tap. It can be long or short, depending on how many threads it spans. Flutes are either straight or spiral. They ensure that the chips produced during cutting can be removed. A further distinction is made as to the direction in which the chips are removed. In the case of right-hand threads, straight flutes and left-hand helical flutes transport the chips in the cutting direction, while right-hand helical flutes transport them against the cutting direction.
Explanation of symbols
D1 = Nominal thread diameter
D2 = Shank diameter
L1 = Total length
L2 = Thread length
□ = Square dimension
Dimensions of machine taps
The construction dimensions of a machine tap are standardized. The various standards specify the overall length of the tool as well as the maximum thread length and define the respective tolerances. A distinction is also made between the shank shape. There are two main shapes that you should be aware of. The overflow shank has the same diameter throughout, while the reinforced shank has a larger diameter than the thread. This means that machine taps with a reinforced shank are not suitable for deep holes, as the tool can no longer penetrate further into the workpiece above a certain depth.
The most common dimensions of machine taps at a glance:
Chamfer for machine taps
The lead of the machine tap is called the chamfer. This is where the main cutting work takes place, so the shape of the chamfer is of great importance. There are six different chamfers, each of which is optimal for certain cases. When buying a machine tap, you should never underestimate the importance of choosing the right chamfer. If you choose the wrong tool, this can have a very unfavorable effect on both the performance and service life of the machine tap and the quality of the thread.
The chamfer form of a machine tap results from several values. The most important of these is the number of threads in the chamfer. This value could also be called the length of the chamfer. The second characteristic is the design of the flutes.
An important factor in the selection of the appropriate chamfer form is the type of core bore. A distinction is made between blind holes and through holes. A blind hole is a hole in which a drill penetrates a workpiece without exiting on the other side. The hole therefore has a fixed depth. A through hole, on the other hand, penetrates the workpiece completely.
Blind hole
With a blind hole, the thread only runs to a certain depth of the workpiece and the component remains closed on the opposite side. This screw connection is particularly stable and ensures high strength. A machine tap for blind holes has a shorter lead chamfer and usually spiral flutes so that the chip can be removed upwards from the hole and no chip jamming occurs. Blind hole taps should not be used for through holes, as they can jam and break when retracted after exiting the hole.
Through hole
A through hole is a hole or thread that passes through the workpiece and forms a continuous opening. A through hole is often used to pass bolts or screws through the part and fix them on the other side. A machine tap for through holes has a longer lead chamfer and usually straight flutes and a spiral point that discharges chips from the bottom of the hole. These features serve to cut through the entire workpiece and allow for faster cutting performance.
The following types of chamfers can be distinguished:
- Form A (6 to 8 flutes, straight flutes): for short through holes
- Form B (3.5 to 5.5 flutes, straight flutes with spiral point): for through holes in medium and long chipping materials
- Form C (2 to 3 flutes, straight flutes or spiral flutes): for blind holes in medium and long-chipping materials and through holes in short-chipping materials
- Form D (3.5 to 5 threads, straight flutes or spiral flutes): for blind holes with long thread run-out and short through holes
- Form E (1.5 to 2 threads, straight flutes or spiral flutes): for blind holes with very short thread run-out
- Form F: for special chamfers with up to 1.5 threads, not recommended
Materials used in the manufacture of machine taps
Machine taps are made of high-speed steel. According to the English designation High Speed Steel, you can recognize this material by the abbreviation HSS. HSS is a very high-quality tool steel and has all the properties that a precise machine tap needs. HSS is very temperature resistant, fracture resistant and allows high cutting speeds.
This group of materials contains steels with different properties. HSSE indicates a steel with an extra alloy of cobalt . The cobalt increases hardness and tempering resistance, but makes the steel somewhat more susceptible to fracture.
The suffix PM does not refer to the composition, but to the manufacturing process of the steel. The abbreviation refers to the powder metallurgical production of steels, which allows higher alloy contents to be set than melt metallurgical production. PM steels combine excellent wear resistance, high hot hardness, and excellent compressive strength with high toughness, isotropic dimensional stability, and good machinability and polishability. If you want to know more about the different materials, you can read about the differences between HSS, HSSE and HSSE-PM here.
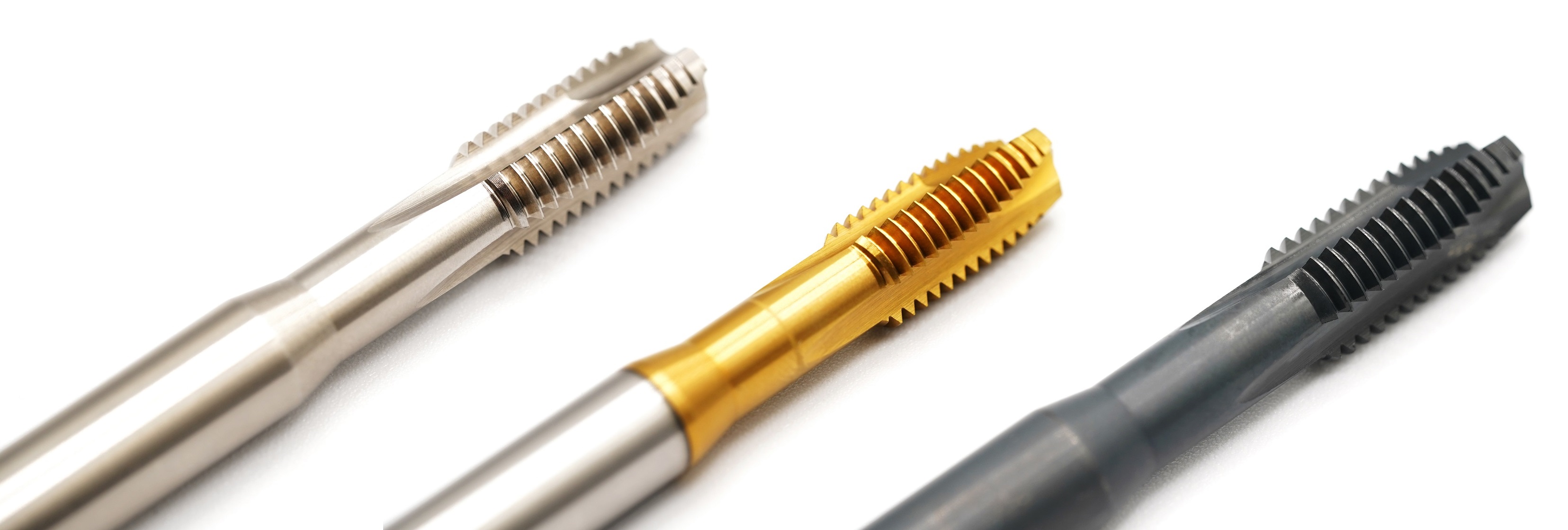
Coatings for machine taps
In addition to the choice of base material, the right coating is a decisive factor in the manufacture of machine taps. Coatings are usually used to increase the wear resistance of the threading tool, improve tool life and corrosion resistance, and enable higher cutting speeds. The choice of coating depends on the material to be worked with. If you are buying a machine tap, you will find corresponding instructions on each product page in the BAER Online-Shop for screw taps.
These are the common coatings used for machine taps:
- Vaporized (VAP): The oxidized surface allows cutting oil to adhere particularly well, providing a constant lubricating film. This prevents cold welding.
- TiN: Titanium nitride increases the surface hardness to approx. 2300 HV and improves the sliding properties.
- TiCN: Titanium carbon nitride increases the surface hardness to approx. 3000 HV and improves the sliding properties.
- TiAlN: Titanium aluminum nitride increases the surface hardness to approx. 3300 HV and improves the sliding properties with a temperature resistance of up to 800°C.
Machine taps at BAER buy - and you're ready to go!
Please also visit our other websites:
We are specialists in threading tools and offer at gewindebohrer.de a wide range of high quality threading tools, such as machine taps, hand taps and thread cutting dies. We place great emphasis on quality and reliability. We also offer threading inserts, drill chucks and other threading products. If you would like to learn more about our other products, please feel free to visit our other websites baercoil.com and bohrfutter.com. Here you will find more information and great offers.
Do you have any questions or would you like individual advice? Then do not hesitate to contact us. Our experienced team will be happy to assist you in selecting the right threading tool for your application.