Threading tool - Surface treatments
Surface treatments are used to make threading tools more wear-resistant and to enable the machining of demanding materials. It is a decisive advantage to only change the surface of a tool. As materials become harder, they also become more brittle. If you only change the surface of a tap, you can improve its hardness without having to compromise too much on toughness. In addition, the surface is the part of the tool that is most exposed to wear effects and environmental influences.
With surface treatments, either the material properties in the outermost material layer are changed using physical or chemical processes or a coating is applied to the threading tool. This allows the properties of the material to be changed in a targeted manner. There are many different surface treatments that make tools more resistant in general or are required for very specific cutting applications. The four most common processes are
TIN (titanium nitride) coating
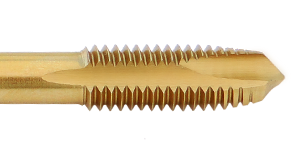
The TIN coating increases the surface hardness to approx. 2300 HV and improves the sliding properties. The tapping tools treated in this way deliver a higher cutting performance and achieve a better tool life. The TIN coating can be recognized by the golden yellow color of the threading tools.
VAP (Vaporized - Vapour activation)
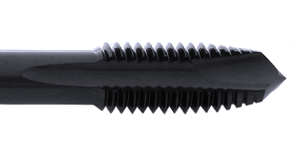
During vaporization, a chemical reaction is triggered by a steam treatment. The surface oxidized in this way (VAP) reduces the sliding resistance and also offers the cutting oil better adhesion. This creates a constant lubricating film, friction is reduced and cold welding can be effectively prevented.
TiAlN (titanium aluminum nitride) coating
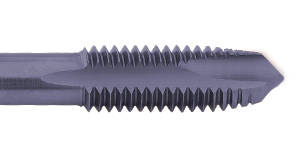
The TiAlN coating increases the surface hardness to approx. 3300 HV and improves the sliding properties (coefficient of friction: 0.25) with a temperature resistance of up to 800°C. This leads to a higher cutting performance and longer tool life. Taps with this coating can also be used at high temperatures in combination with limited cooling possibilities. TiAlN-coated tools can be recognized by their purple color.
TiCN (titanium carbonitride) coating
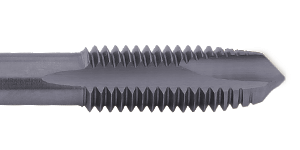
The TiCN coating increases the surface hardness to approx. 3000 HV and improves the sliding properties (coefficient of friction: 0.3). It produces a higher cutting performance and tool life even under high mechanical loads, e.g. when used for high-strength steels and abrasive materials. However, TiCN-coated taps have a lower heat resistance and must therefore be sufficiently cooled. They can be recognized by their grey-violet color.
Coating service
Every threading tool in our product range - whether cataloged or not - can be supplied at short notice with any coating or surface treatment.